Changes to the 737 MAX / Return to Service
Return to Service
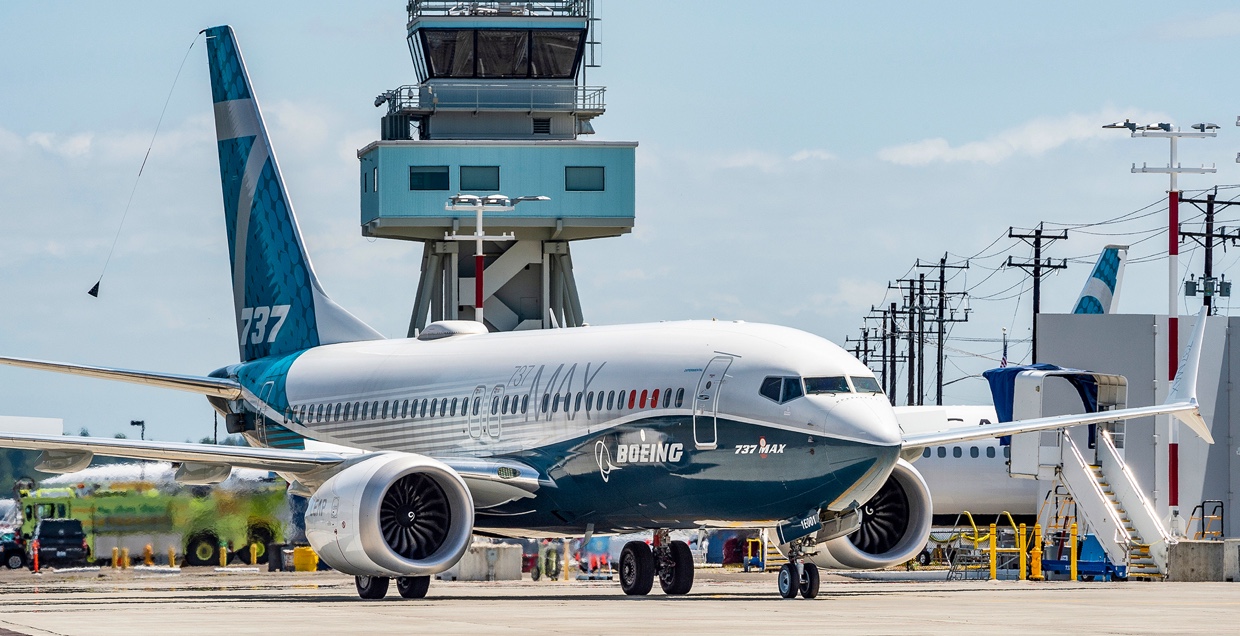
How were the airplanes prepared?
How were regulators involved in the process?
Regulators’ requirements set out a careful and documented process that defined how airplanes are to be removed from storage and reactivated, what work is performed on them, and how they must be inspected and approved prior to returning to commercial service.
How long does the process take?
Safety is the most important priority, so each part of the process was given the time needed for it to be accurately completed and fully documented to regulators’ standards.
What was required to take the airplane out of storage?
When each airplane was stored, it went through a comprehensive multi-day process designed to preserve the airplane and its engines and systems while not in use. The process has to be reversed before the airplane could be reactivated.
What work was performed on each airplane?
Once the airplane was reactivated, all of the changes mandated by regulators were completed and thoroughly documented. Those included updates to MCAS, additional software updates, and modifying some wiring to meet regulators’ requirements.
What did inspecting the airplanes entail?
Regulators defined the comprehensive processes used to inspect and approve each and every airplane before it returned to commercial service.
What will happen with the undelivered airplanes that are still at Boeing?
Every airplane will go through Boeing’s comprehensive protocol for delivery of a new airplane. This includes flight-critical ground testing, test flights by Boeing and the customer, and a detailed customer inspection. The FAA will perform in-person, individual reviews of each new airplane prior to issuing its airworthiness certificate.
What will happen with the airplanes that were delivered to customers?
Airplanes that are already part of a customer fleet had their own processes and checkpoints. These included showing the local regulator documentation of all of the performed changes and completing an operational readiness flight.
How are you supporting the airlines?
We support our customers every day for every Boeing airplane they fly.
What kind of support did you provide while 737 operations were suspended?
Our support for customers flying the 737-8 and 737-9 never stopped. We continued to work with each of them to resolve any challenges or questions as they arose. To keep all of our customers informed about the latest developments in process and status, we also set up an information-sharing program, where we would provide a full update every week. We also conducted monthly collaborative work sessions with our global community of airline partners.
As the airplanes began to transition into long-term storage, we set up a proactive approach where we regularly visually inspected every one of the stored airplanes, regardless of its location around the world. Our inspector would document their findings and share it with the airline and the larger community of partner airlines.
Whenever an airline had to ferry a stored airplane to another location, we worked alongside their team to remove the airplane from storage, reactivate it and monitor all of its systems while in-flight. Ultimately, more than 400 flights were conducted, generating invaluable data about the process and performance of the reactivated airplane.
What kind of support did you provide as airlines returned their airplanes to service?
There are three fundamental areas of support.
24/7 dedicated operations center
We are staffing a cross-functional team that represents all of the engineering and technical areas involved with the airplane. The team works around the clock, providing real-time solutions to any challenges a customer may face and provide real-time monitoring of all 737-8 and 737-9 airplanes in flight.
Onsite support
We expanded our existing field-service teams with additional staff that can be deployed to help an airline complete and document every step of the comprehensive process mandated by their regulator.
Global parts support
We identified the specific parts that the airlines might require when reactivating the airplane. We increased our stock accordingly and deployed the parts in advance to our regional distribution centers around the world so that they were nearby if needed.