From rowing to Boeing
In the days of wooden boats and airplanes, craftsmanship proves worthy of medals and merit.
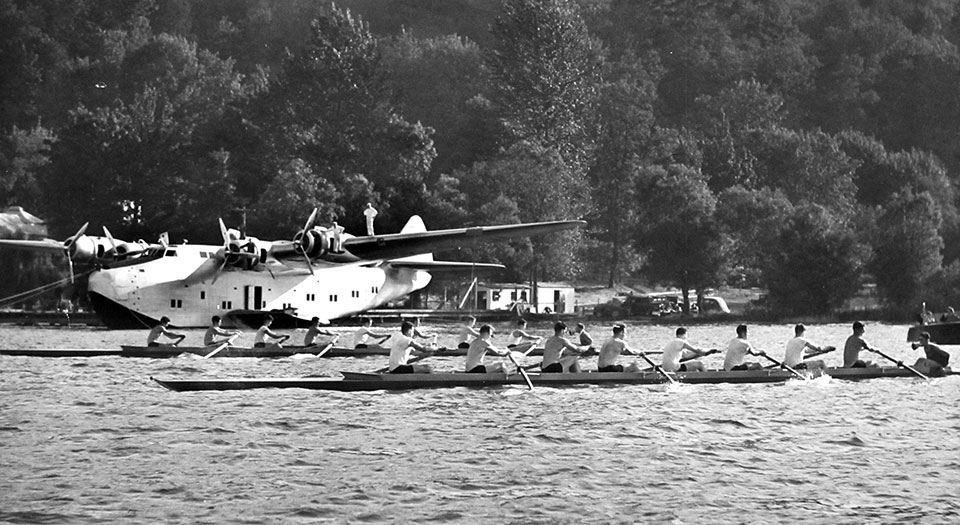
When brothers George and Richard “Dick” Pocock moved to Seattle in 1912 to build racing shells for the University of Washington, they didn’t anticipate where their woodworking skills would take them.
In a copy of his unpublished memoir kept in the Boeing Archives, George describes the unusual circumstances that led the company’s founder, William E. Boeing, to hire the Pococks away from boat building and into aviation history.
It is now early 1916, and one afternoon the president of the university came in the old Tokyo Tearoom shop. He had a gentleman with him.
“These are the boys I was tellin’ you about, Bill,” he said. We had a new finished eight in the shop, which was to go to California. Bill whoever-he-was got under the boat and was on his knees really interested.
“This is the very work I want,” he said to Dr. Henry Suzzallo, the president.
President Suzzallo by now was at the door, tapping the floor with his cane and saying, “Come on, Bill, I must go.”
Bill got up on his feet and started for the door with his hand in his pocket. Taking out his card case, he threw a card on the bench and said, “Come and see me as soon as you can.”
We looked at the card to see who Bill was. The card read W.E. Boeing, Hoge Building, Seattle. We had heard that a man by that name was building a seaplane for his own private use and this undoubtedly was the man.
Boeing turns to brothers to build flying boats
Not long after Boeing’s visit to the university, in 1917 he received an order for 50 Model C trainers for the U.S. Navy. He hired the Pocock brothers, who brought on 12 more employees to help them construct pontoons for the seaplanes. They set up production in Plant 1, the “Oxbow” plant, which affectionately became known as the Red Barn and is now preserved at The Museum of Flight in Seattle.
Soon the team was producing one pontoon per day in the same shop where Boeing was building Curtiss HS-2L flying boats, bedroom furniture and flat-bottomed boats known as sea sleds. George discovered the vertical grain western red cedar was a far better material to plank the flying boats. Using western red cedar made the pontoons lightweight but strong enough to land on water.
When airplane production slowed to a standstill in 1919, the Pococks honed their woodworking skills on a couple of shells in an unused space in the Red Barn.
In 1922, the brothers left Boeing and returned to boat building. George set out on his own and built racing shells for UW, while Dick built shells at Yale.
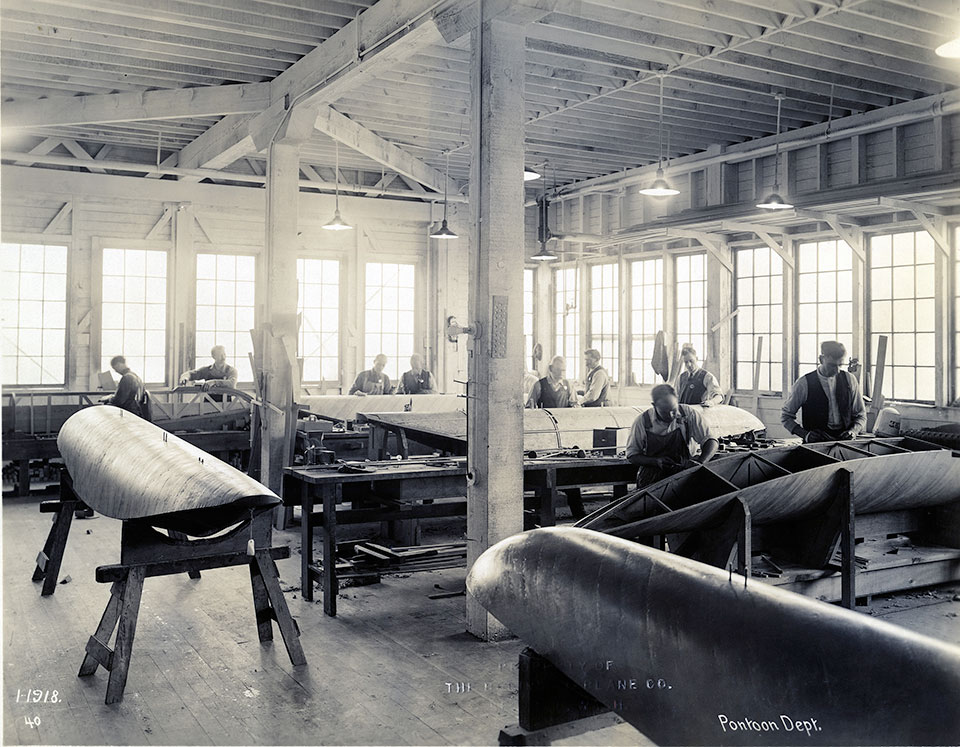
About this time Dick and I took ourselves off the Boeing payroll and built a couple of eight-oar’d shells in one of the unused shops. When finished they were put over in the new H.S.2 assembly room. It was now 1919.
The aircraft industry was virtually at a standstill. Boeing did not have a tap of work to do on airplanes. The engineering department consisted of three men and a young woman designing a couple of models.
A House committee from Washington, D.C., was touring the country visiting all plants that had built airplanes during the war to see which ones were worthy of keeping running, I supposed. The committee arrived at Boeing and there was nothing to see except some drawings of airplanes. They toured the whole plant: machine shops, plating shop, wing room, woodworking room, and lastly they went over to the huge, as we thought then, final assembly building. There were the two eight-oar’d shells Dick and I had built – 60 feet long, but still lost in such a big place.
One member of the committee hurried over to the two boats and walked up and down in amazement.
“Who on earth built these?” he asked Edgar Gott, the general manager.
“Oh, two of the boys who work for us.”
The committee man said, “I rowed at Harvard and I never expected to see anything like this out here. I would like to meet the builders and talk to them.”
So we were sent for and a pleasant chat ensued on rowing, not airplanes. Mr. Gott was excited. By then all the committee were studying the boats and incidentally admiring the workmanship, which was pretty good.
“That’s the kind of workmen we have here,” Mr. Gott told the committee.
It could not have done any harm for very shortly thereafter, the company received an order for 200 pursuit planes, and as Mr. Boeing had predicted, they never looked back.
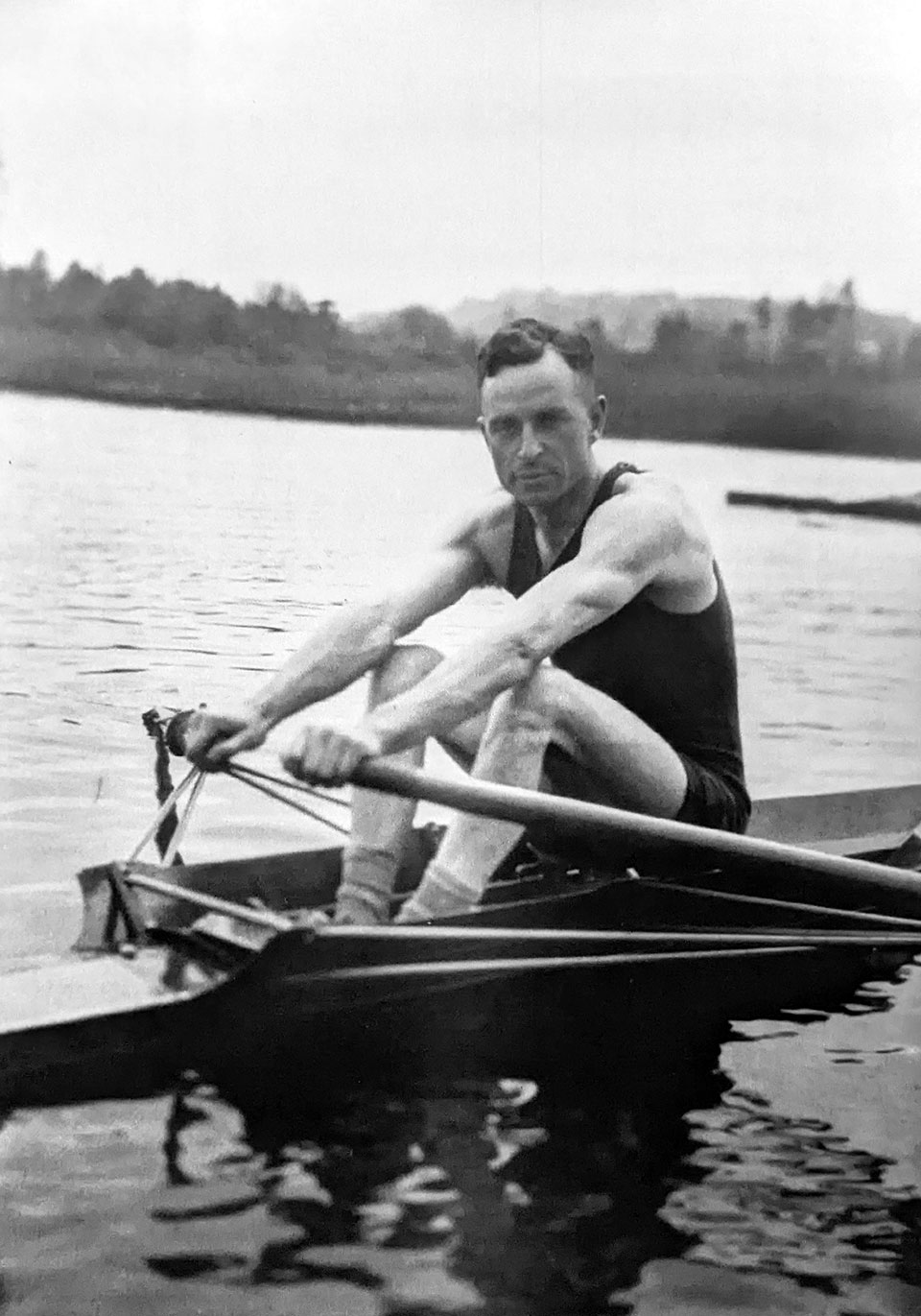
Building boats for The Boys of 1936
Soon after George began building eight-oared shells for UW in the university’s Shell House, the UW varsity 8 crew won its first national championship in a Pocock shell. Over the next decade, the team earned national prominence, with the undefeated UW varsity 8 crew winning its first collegiate 2,000-meter national championship in 1933, besting Yale, Cornell and Harvard.
In 1936, UW achieved another first in collegiate rowing — a sweep of the Intercollegiate Rowing Association National Championship, with the freshmen, junior varsity and varsity 8 crews claiming victory. Undefeated, the varsity 8 crew qualified for the 1936 Olympic Games in Berlin.
With fans proclaiming the UW team the best crew to ever race, the team won Olympic gold in a Pocock shell in an extraordinarily close finish right in front of the main grandstands.
Just a few years later, the U.S. entered World War II.
As a subcontractor, George Pocock again applied his woodworking skills to aircraft, building floorboards for Boeing B-17 bombers.
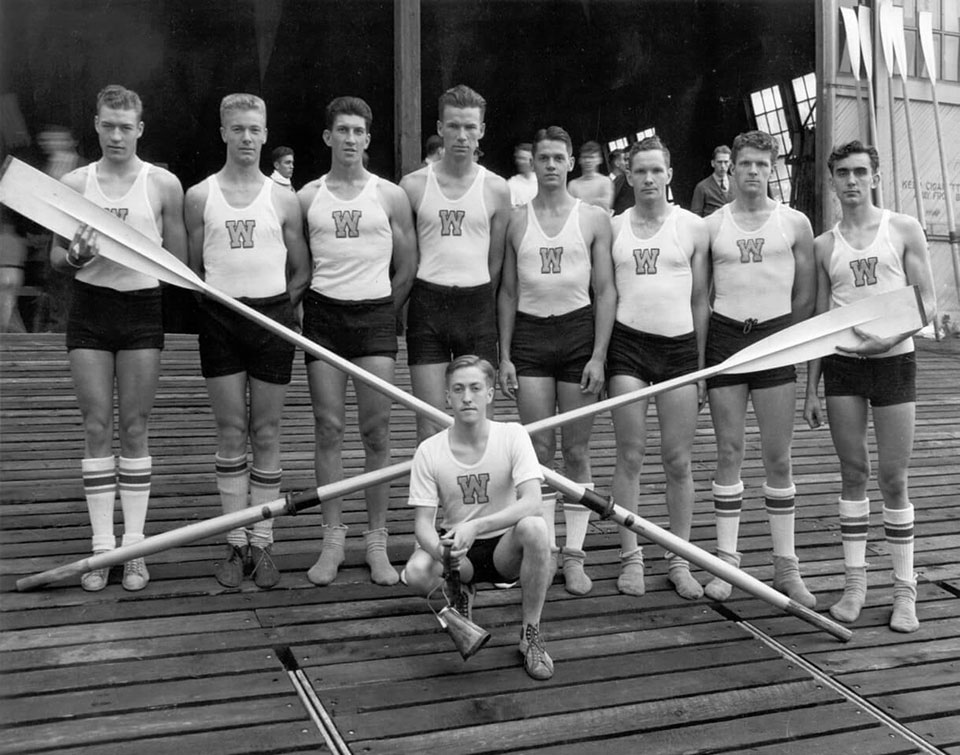
The Boys of 1936
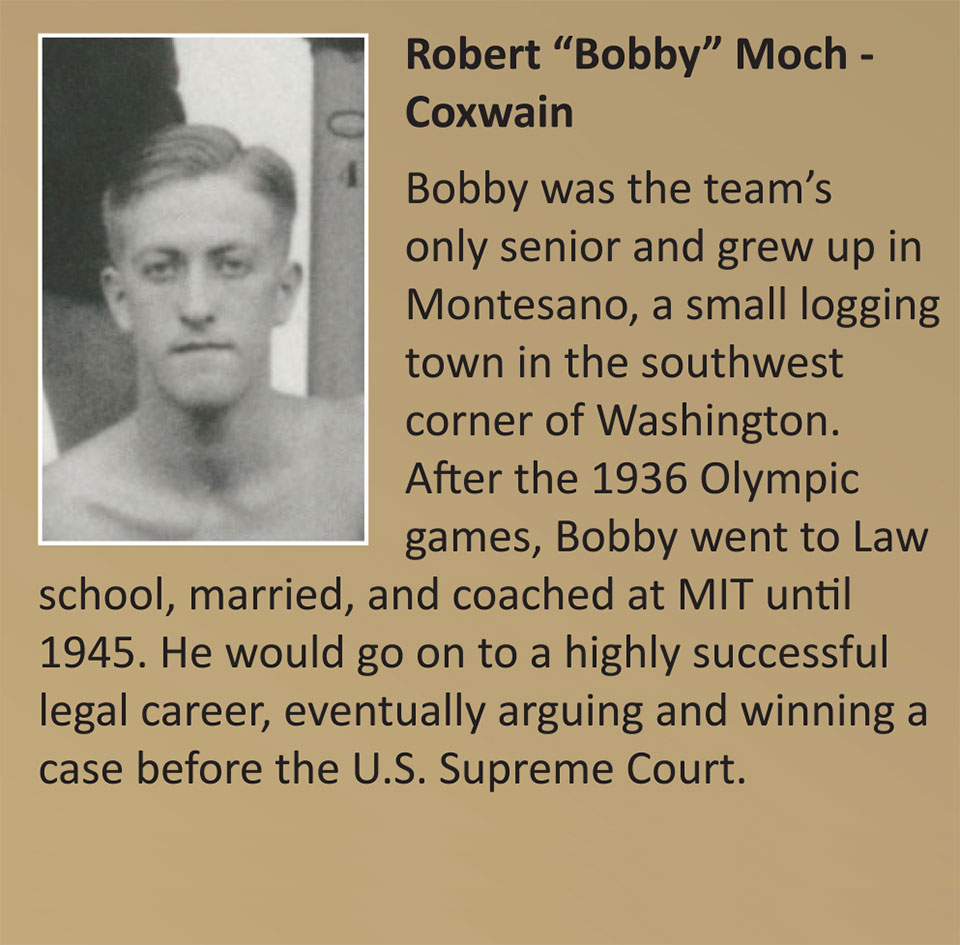
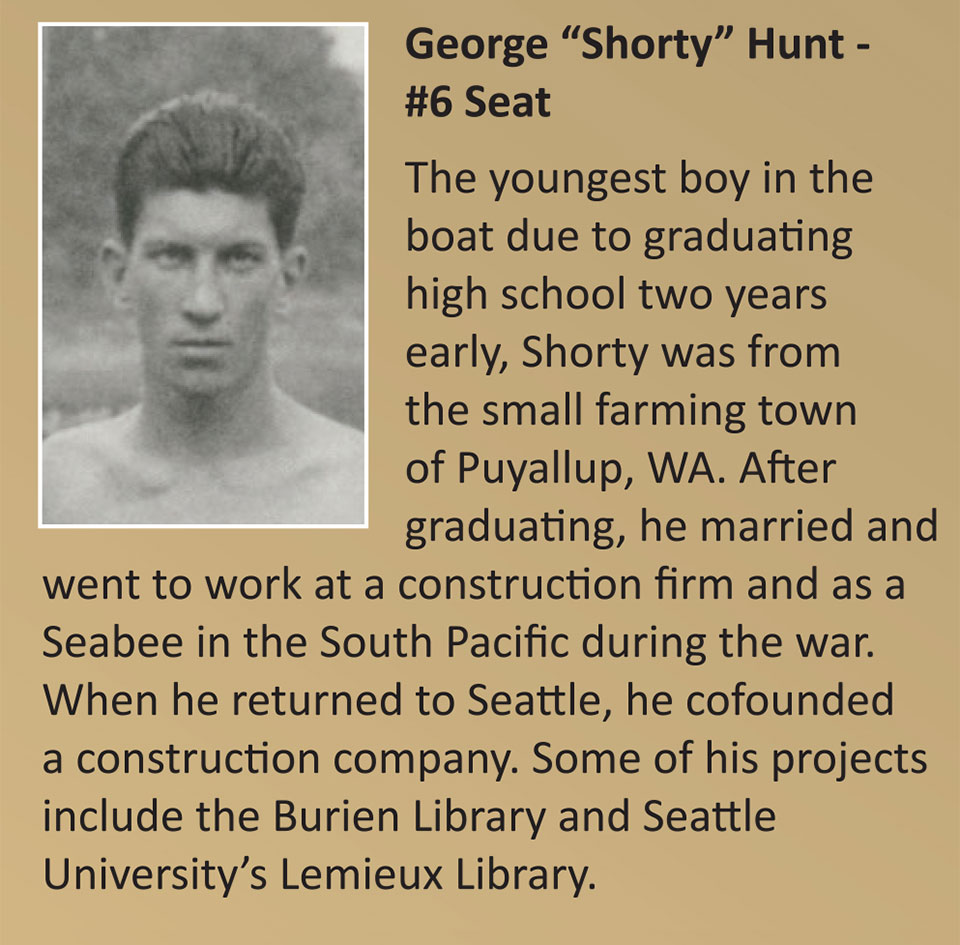
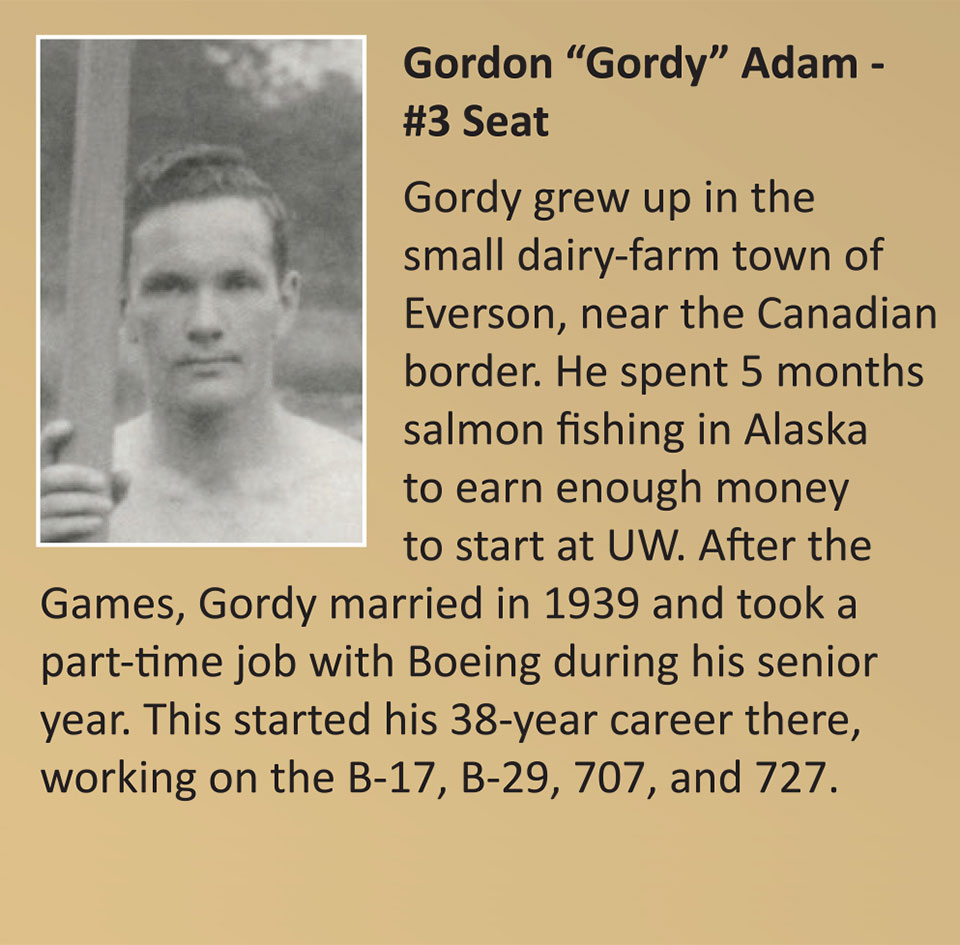
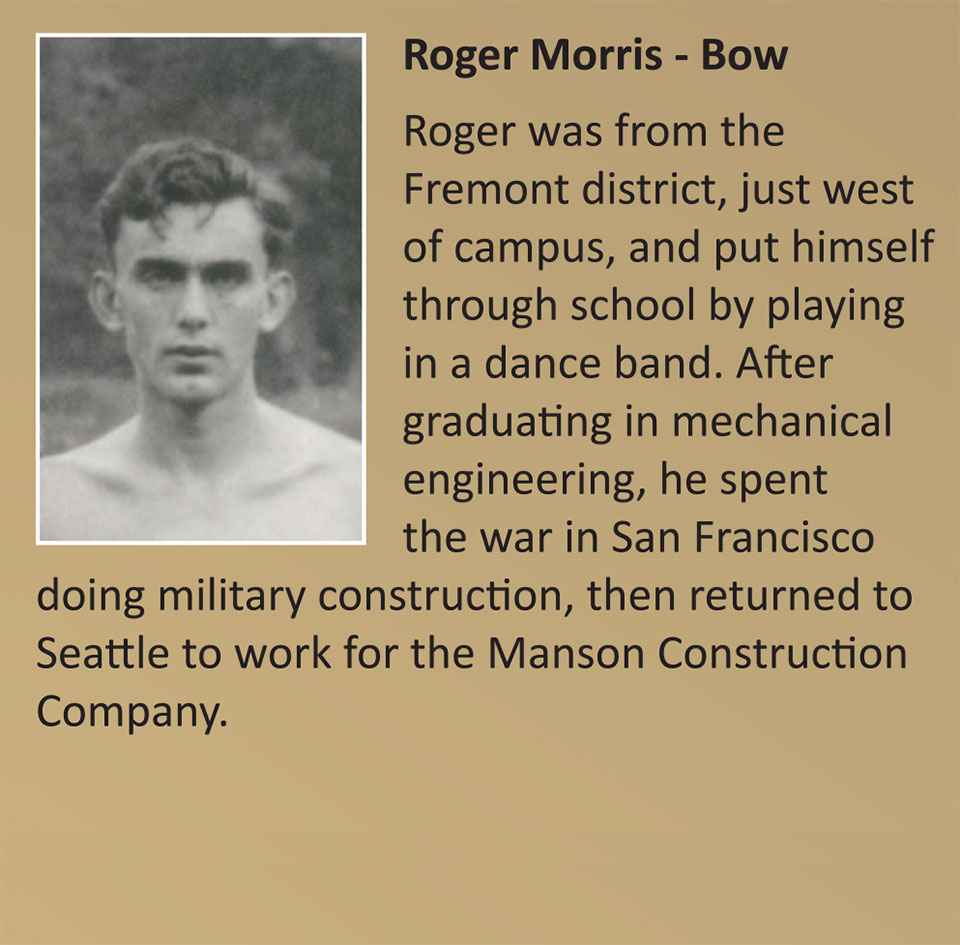
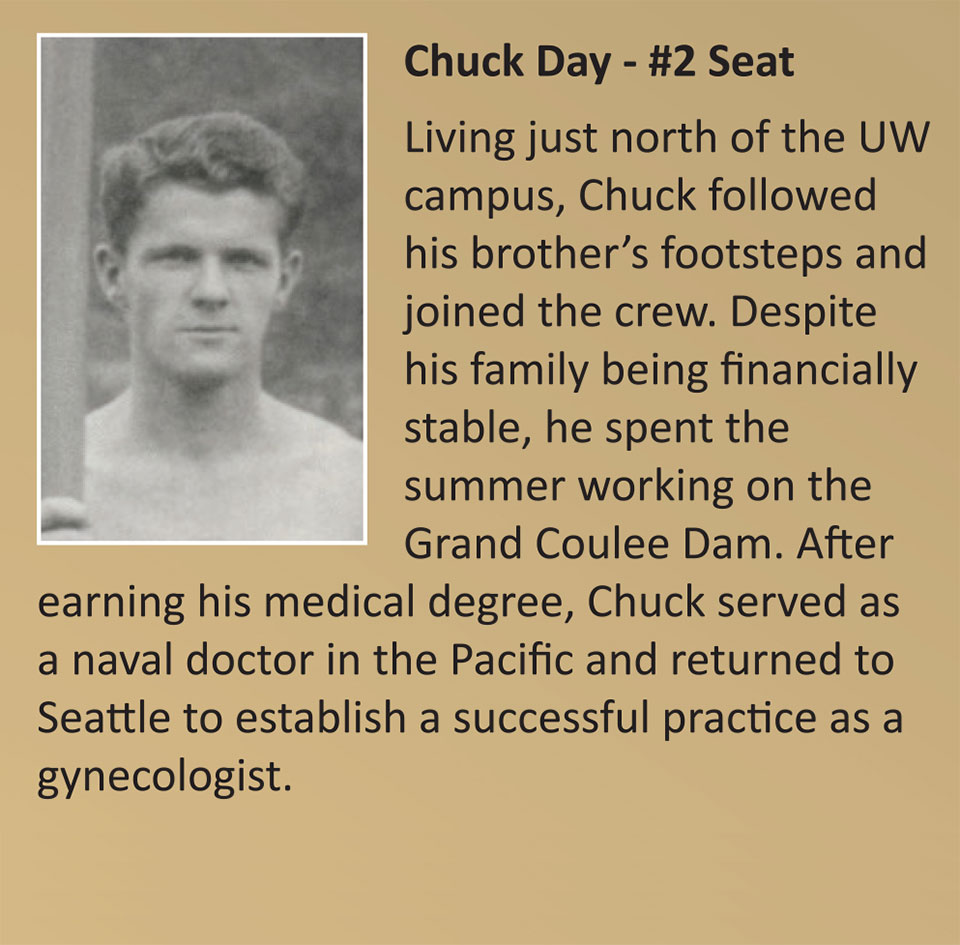
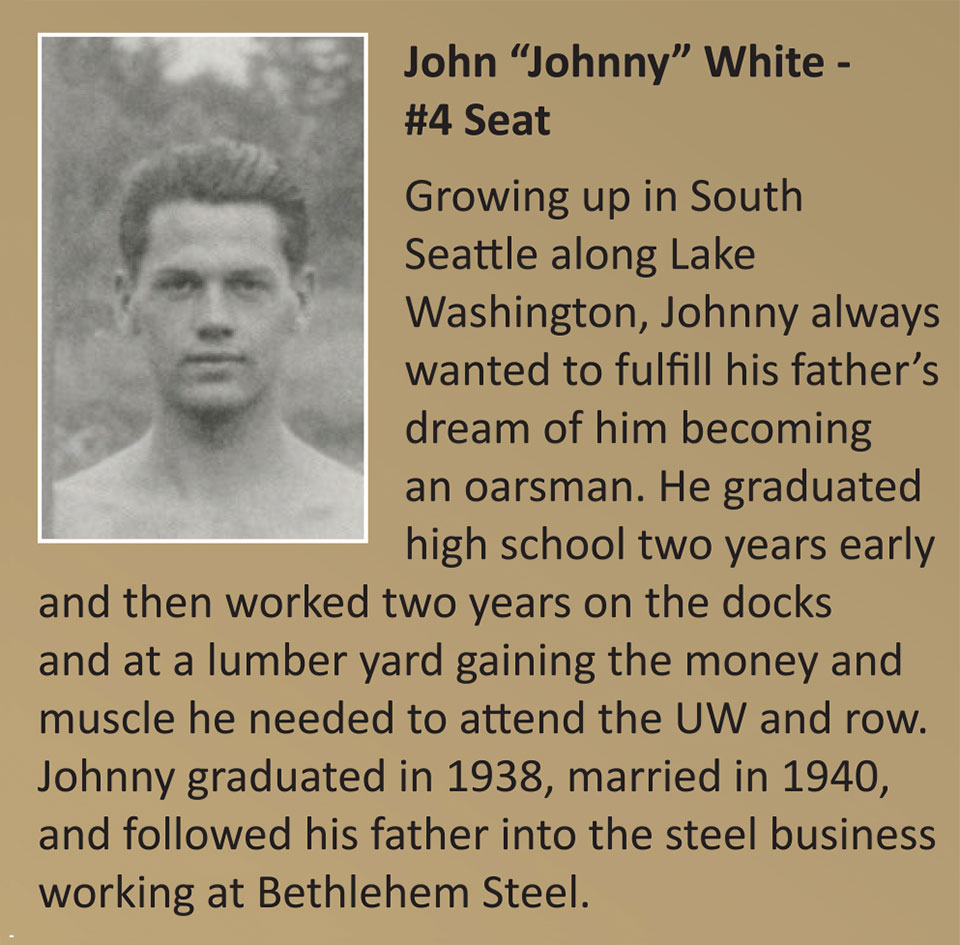
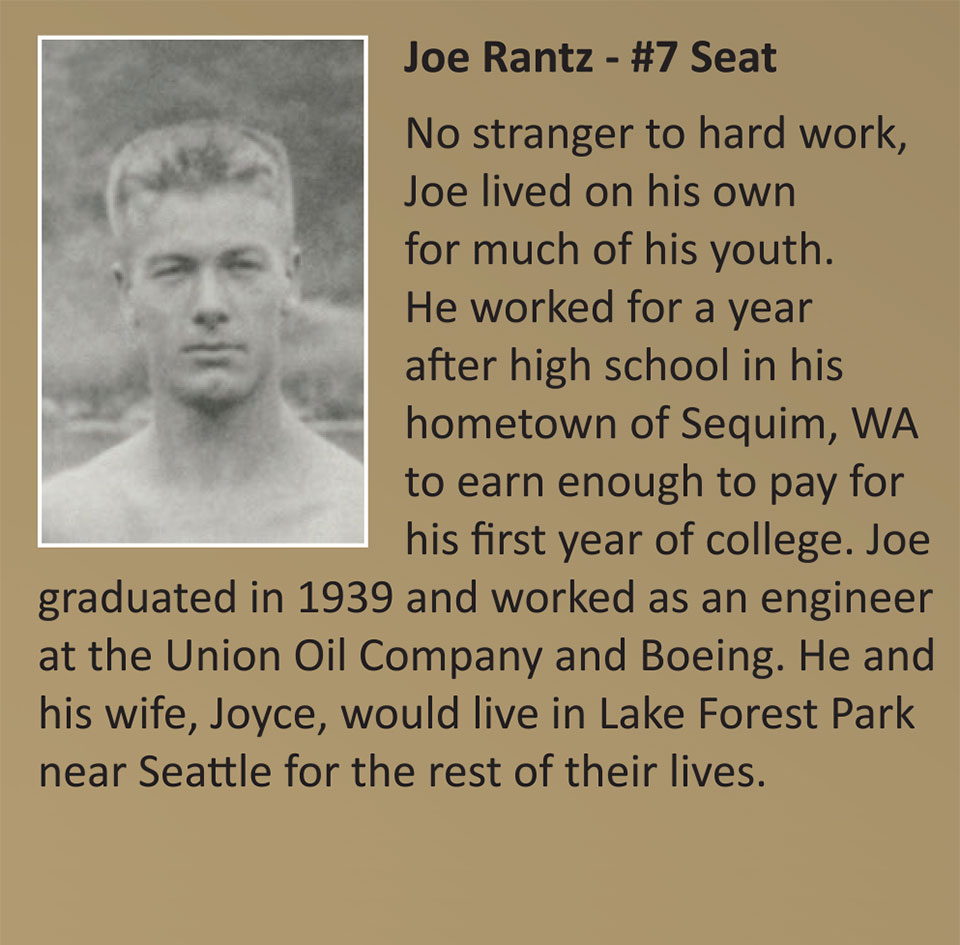
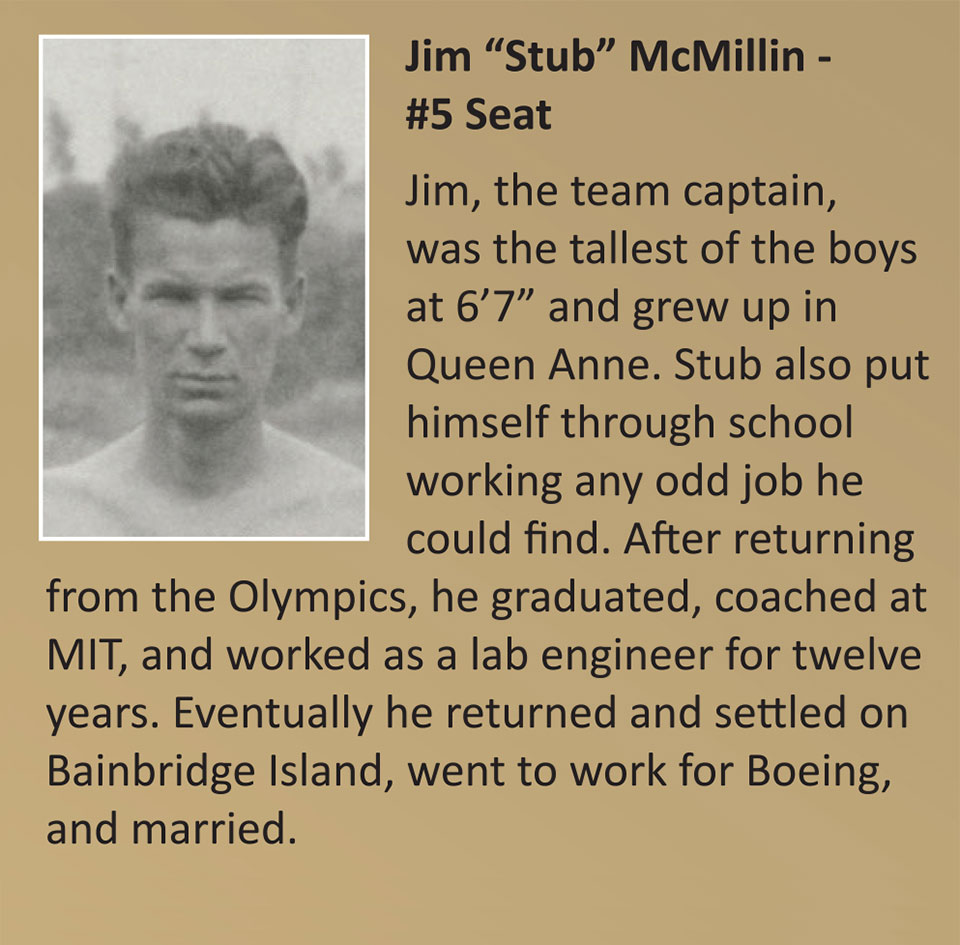
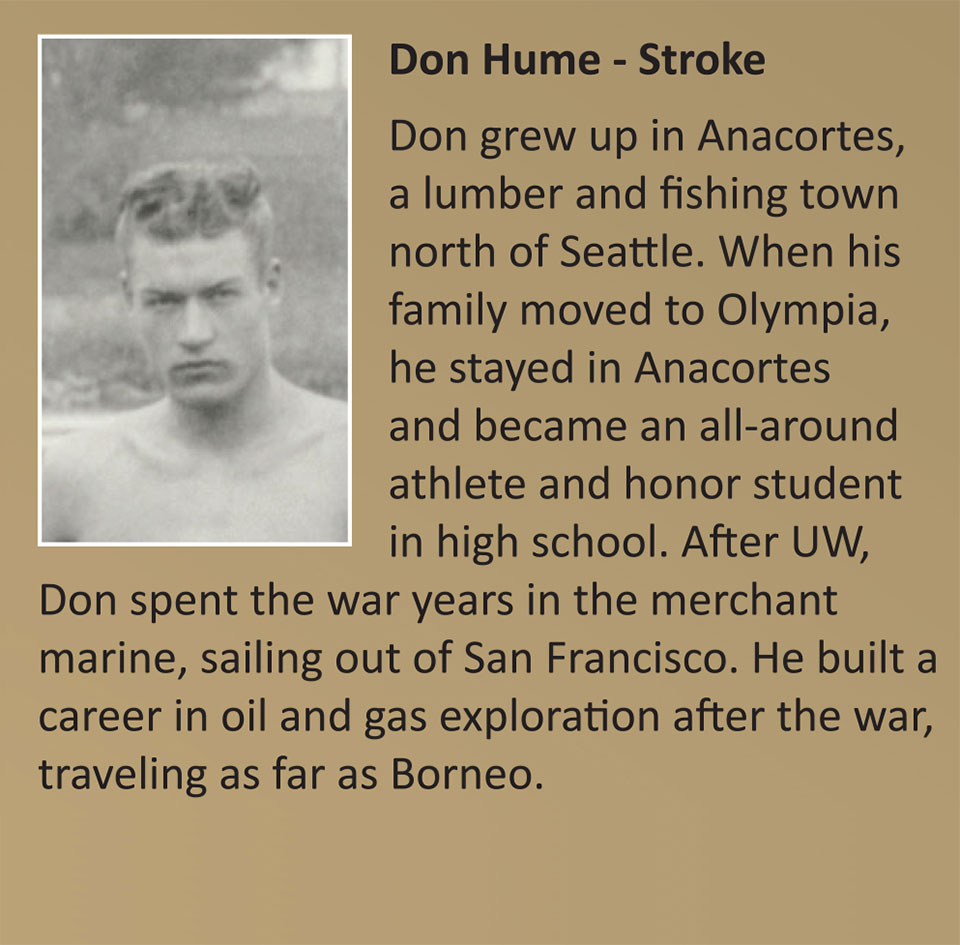
- Image 1
- Image 2
- Image 3
- Image 4
- Image 5
- Image 6
- Image 7
- Image 8
- Image 9
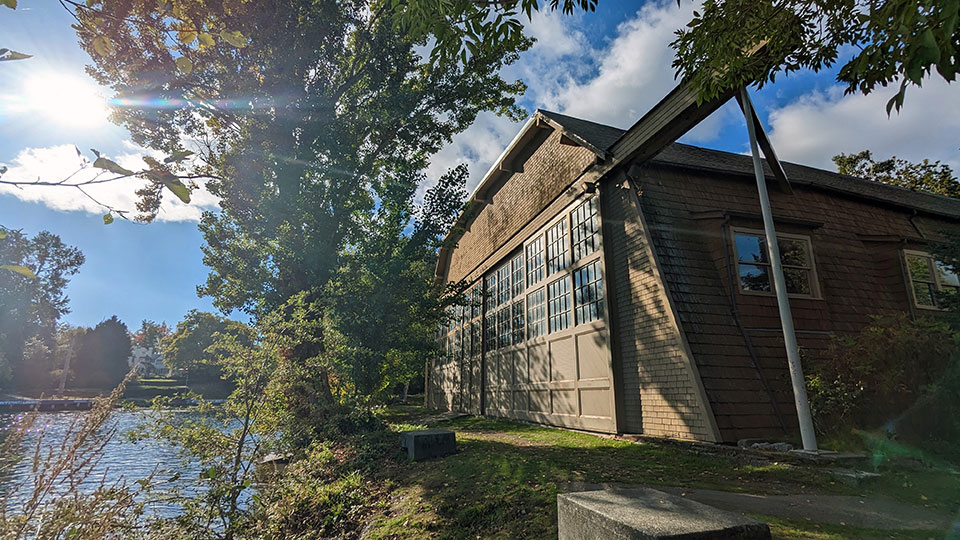
Hangar is centerpiece of rowing history
The Associated Students of the University of Washington (ASUW) Shell House stands today on the shores of Lake Washington. Indigenous Coast Salish residents called the site stəx̌ ʷugʷił (stukh-ug-weelth), or “carry a canoe.”
Originally constructed to house seaplanes and train aviators during World War I, the building is one of only two such original hangars still in existence. The facility is the centerpiece of a project to preserve the historic building and transform the waterfront area into an inspirational cultural center.
Following World War I, the university converted the hangar into the Washington Rowing boathouse. In the early 1920s, UW added an interior upstairs loft workshop for George Pocock. There, in a space just 65 feet (20 meters) at its widest, Pocock constructed the racing shells for the UW crew champions and the 1936 Olympic gold medalists.
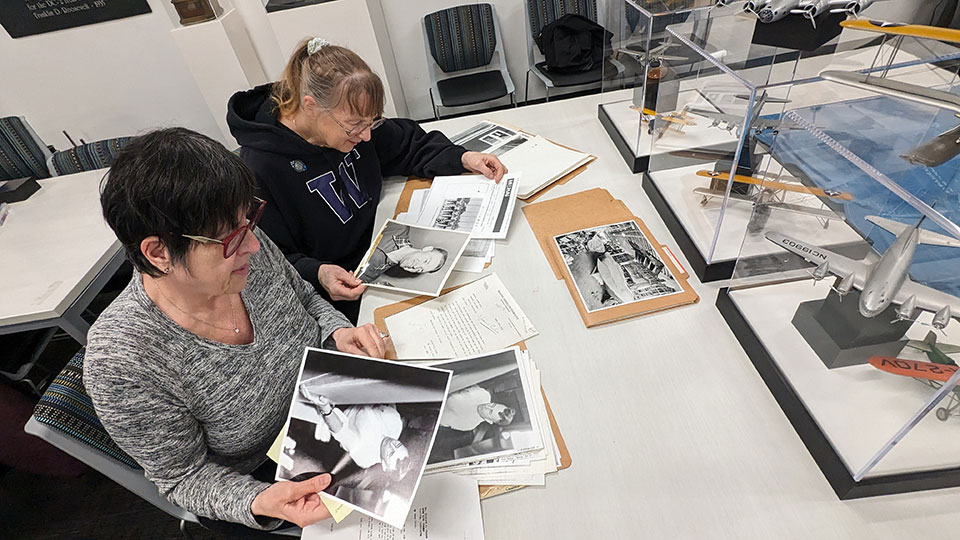
Olympic champions, Boeing teammates
All nine team members survived the war. Years later, as stories about their Olympic victory were told and retold, Joe Rantz especially emphasized the win was a team effort. As a team, the UW varsity 8, known at the university as “The Boys of 1936,” was undefeated.
Three members of the 1936 Olympic team became Boeing teammates. Gordon Adam enjoyed a 38-year career at Boeing, serving as a supervising engineer in the 707/727 program. Jim McMillin worked as a unit chief in electrodynamics instrumentation technology. Rantz was a chemical engineer.