Jig is up: Holding tight to ensure quality parts
The contour assembly jig plays a critical role in creating the 737 MAX lipskin, the leading edge of the engine nacelle.
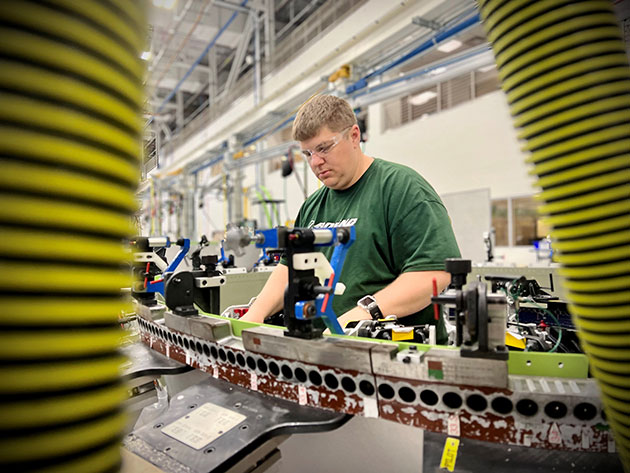
Hand-like clamps emerge from the large metal hoop, ready to hold tight the metallic structure that will be formed into precise dimensions to create critical aviation structure.
The required shape is defined by experienced engineers, controlled by modern automation, created by skilled technicians and validated by precision equipment. But nothing is more crucial to the capability to achieve success than the tooling at the center of it all – the contour assembly jig.
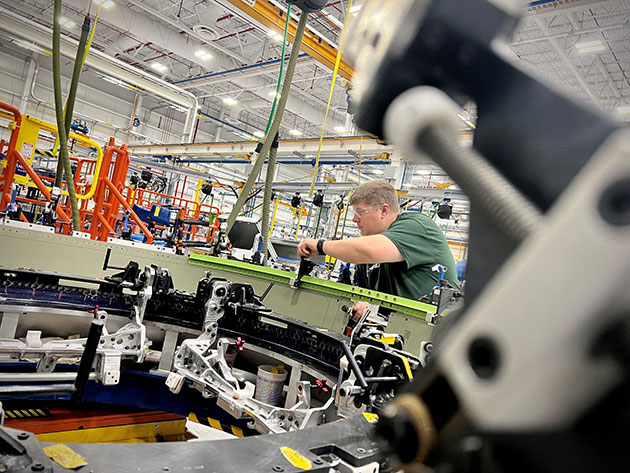
At Boeing’s Propulsion South Carolina facility, technicians stand in the center of the jig, designed specifically for the creation of the leading edge of the 737 MAX engine nacelle, known as the lipskin.
Share this story, and inspire someone to join Team Boeing! Explore job opportunities, internships and more at Careers at Boeing.
Teammates, like Howard Leonard, use the tool to precisely align components of the lipskin, then “drill and fill” more than 300 holes with rivets and fasteners that withstand decades of travel, tens of thousands of feet in the air and at speeds of more than 80 percent the speed of sound.
“It’s a cool piece of the factory because there’s so many moving parts that come together in this culmination of technology to make what would be an otherwise difficult task into a fast, predictable and efficient process,” said Leonard, a U.S. Navy veteran.
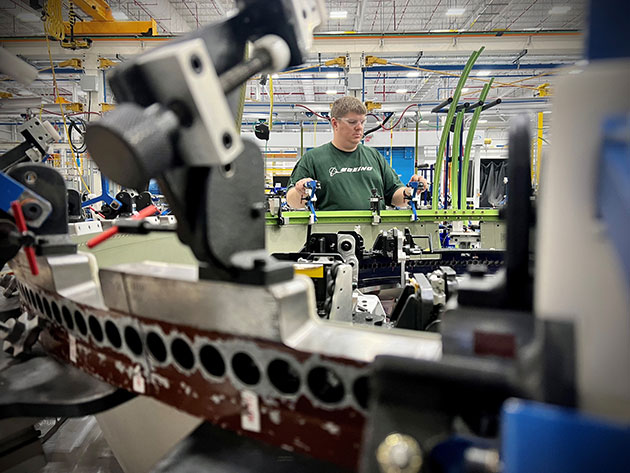
The tool utilizes 20 independent, movable fixtures that allow the mechanic to establish and maintain the lipskin’s engineered frame, which is approximately 7 feet (2.13 meters) wide.
“This is probably one of the more complex, automated tools we have here,” he adds. “If we can design and develop the automated contour jig we have today with all of its current capabilities, the future is bright for what we come up with next.”
Leonard says he’s been fascinated with airplanes from a young age and working at Propulsion South Carolina has helped him achieve his dream of working in the aerospace industry.
“Every time I see a 737 MAX, I have an overwhelming sense of pride knowing I have had a hand in making these airplanes a reality,” Leonard says.
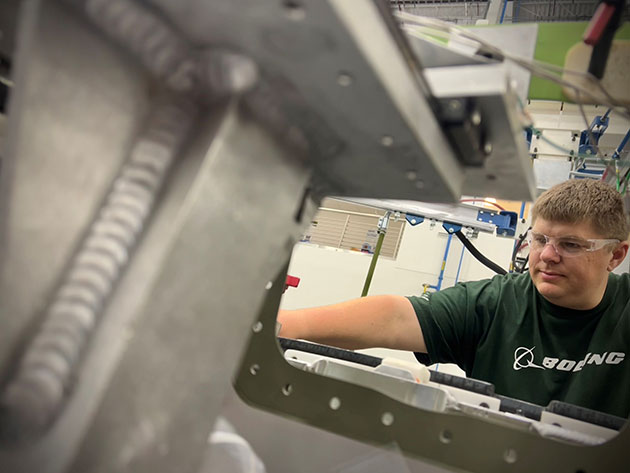